Most business challenges are not caused by a lack of strategy, but by breakdowns in execution. When work slows down or projects miss deadlines, the problem often lies within the hidden, everyday workflows that power your organization. These invisible inefficiencies create friction, waste resources, and prevent teams from performing at their best.
Process analysis provides a systematic way to uncover and fix these issues by creating a clear map of how work actually gets done. This guide covers the essential steps for conducting an analysis, key techniques like value stream mapping, and the tools that support lasting improvement. We will explore how to identify bottlenecks, measure performance, and implement changes that deliver real results.
By applying this framework, you can build more resilient and efficient operations. You will learn how to spot waste, improve quality, and align your team’s daily activities with strategic goals, creating the foundation for continuous improvement.
Try monday work managementKey takeaways
Before diving into the details, let’s review the essential concepts you’ll learn from this guide.
- Process analysis is the systematic examination of workflows that reveals hidden inefficiencies, bottlenecks, and improvement opportunities by mapping each step from start to finish.
- The seven-step framework — identify, map, evaluate, pinpoint bottlenecks, propose improvements, implement, and monitor — provides a proven approach to transform how work flows through your organization.
- Different analysis techniques like flowcharts, value stream mapping, and SIPOC serve specific purposes, helping you choose the right method based on what you need to understand about your processes.
- Common challenges including stakeholder resistance, incomplete data, and process complexity can be overcome with proper preparation, stakeholder involvement, and focusing on high-impact processes first.
- monday work management transforms traditional process analysis into ongoing optimization with AI-powered bottleneck detection, real-time dashboards, and automated insights that help you spot issues faster and maintain improvements over time.
What is process analysis?
Process analysis is the systematic examination of how work gets done in your organization. It means breaking down complex workflows into individual steps to understand what happens, who does it, and where problems occur.
Think of it as creating a detailed map of your work. You document each action, decision point, and handoff to see the complete picture of how things flow from start to finish.
The core components that make process analysis work include:
- Process mapping: Creating visual diagrams of your workflows
- Data collection: Gathering real information about how long things take and where delays happen
- Gap identification: Finding the difference between how things work now and how they should work
- Improvement planning: Developing specific actions to fix problems
How does this impact your business? Process analysis reveals the hidden inefficiencies that slow you down and cost money. It shows you exactly where work gets stuck and helps you make informed decisions about what to fix first.
Why process analysis matters for business success.
Every organization has workflows that could work more smoothly. Process analysis gives you the power to see these opportunities clearly and act on them.
When you understand your processes, you can spot where time and money disappear. Maybe approvals take too long because 5 people need to sign off when 2 would suffice. Perhaps your team duplicates work because departments don’t communicate effectively.
The real value comes from turning these insights into competitive advantages:
- Faster delivery: Remove bottlenecks that slow down your projects
- Cost reduction: Eliminate redundant steps and wasted resources
- Quality improvement: Build consistency into how work gets done
- Strategic alignment: Connect daily activities to business goals
Through real-time dashboards, monday work management provides the visibility you need to make smart decisions about resources and priorities. It helps you identify improvement opportunities.
7 steps in the analysis process.
Follow this proven framework to conduct thorough process analysis that delivers real results. Each step builds on the previous one to create a complete understanding of your workflows.
Step 1: Identify the process.
Start by choosing which process to analyze. Focus on workflows that affect multiple teams or directly impact customers. Look for processes that people complain about or that consistently miss deadlines.
Consider these factors when selecting your target:
- Frequency: How often does this process run?
- Impact: How many people or customers does it affect?
- Pain level: How much frustration does it cause?
- Strategic importance: Does it connect to key business goals?
Step 2: Gather and map data.
Now document how the process actually works — not how it’s supposed to work. Talk to the people who do the work every day. Watch them complete tasks. Collect data from your systems.
Create a visual map showing each step, who does it, and how long it takes. Include decision points, approvals, and handoffs between teams.
Step 3: Evaluate current efficiency.
Measure your process performance using concrete metrics. Track cycle times, error rates, and how often work needs to be redone. This baseline data proves whether your improvements actually work.
Common metrics to track include:
- Cycle time: Total time from start to finish
- Touch time: Actual work time versus waiting time
- Error rate: How often mistakes happen
- Rework rate: How often you need to fix things
Step 4: Pinpoint bottlenecks.
Look for places where work piles up or slows down. These bottlenecks often occur at approval points, when switching between teams, or where resources are limited.
Ask yourself: Where does work sit waiting? Which steps take longer than they should? Where do errors most often occur?
Step 5: Propose improvements.
Develop specific solutions for each problem you identified. Focus on changes that address root causes, not just symptoms. Consider automation for repetitive tasks and clearer handoffs for communication issues.
Step 6: Implement changes.
Roll out improvements gradually. Start with a pilot test to work out problems before full implementation. Communicate clearly about what’s changing and why. Train people on new procedures.
Step 7: Monitor and adjust.
Track your metrics to see if improvements work as expected. Be ready to adjust based on real results. Process improvement never really ends — it’s an ongoing cycle of refinement.
monday work management supports every step of this process with features like workflow templates, automated data collection, and real-time performance dashboards that make monitoring effortless.
Essential process analysis methods and techniques.
Different analysis techniques serve different purposes. Choose the right method based on what you need to understand about your processes.
Flowcharts and diagrams.
Flowcharts use simple shapes to show how work moves through your organization. Rectangles represent tasks, diamonds show decisions, and arrows indicate flow direction. This visual approach makes complex processes easy to understand.
Flowcharts excel at revealing:
- Redundant steps: Tasks that don’t add value
- Missing connections: Where handoffs fail
- Decision complexity: Too many approval layers
Value stream mapping.
Value stream mapping distinguishes between activities that add value for customers and those that don’t. This lean methodology helps you focus improvement efforts where they matter most.
The technique shows you:
- Value-added time: Work that directly benefits customers
- Wait time: Delays between steps
- Waste: Activities that consume resources without adding value
BPMN and swimlane models.
Business Process Model and Notation (BPMN) provides a standardized way to document processes. Swimlane diagrams show which department or role handles each step, making cross-functional workflows crystal clear.
These models help you see:
- Role clarity: Who’s responsible for what
- Handoff points: Where work moves between teams
- Parallel activities: Tasks that can happen simultaneously
SIPOC and other practical tools.
SIPOC (Suppliers, Inputs, Process, Outputs, Customers) gives you a high-level view of any process. Start here when you need to understand the big picture before diving into details.
Other useful techniques include:
- Root cause analysis: Dig deep to find why problems really occur
- Time studies: Measure exactly how long tasks take
- Process observation: Watch work happen in real time
monday work management integrates these analytical approaches into your daily workflow, letting you map processes, track performance, and implement improvements all in one platform.
Try monday work managementHow to apply process analysis in different industries.
Process analysis principles work everywhere, but implementation varies by industry. Here’s how to apply these techniques in your specific context.
Manufacturing and production.
In manufacturing, process analysis focuses on production flow, quality control, and equipment utilization. You’ll examine how materials move through your facility, where defects occur, and which machines create bottlenecks.
Key areas to analyze:
- Production scheduling: How orders flow through your system
- Quality checkpoints: Where and how you inspect products
- Inventory movement: How materials travel from receiving to shipping
Business operations.
Administrative processes often hide the biggest improvement opportunities. Analyze workflows like expense approval, contract management, and project initiation to find delays and redundancies.
Common operational processes to examine:
- Approval workflows: How decisions move through management layers
- Document handling: How information flows between departments
- Resource allocation: How you assign people and budgets to projects
Service and customer support.
Service processes directly impact customer satisfaction. Map customer journeys, analyze response times, and identify where service breaks down.
Focus your analysis on:
- Ticket routing: How requests reach the right person
- Resolution paths: Steps to solve common problems
- Escalation procedures: How complex issues move up the chain
monday work management adapts to any industry, providing customizable templates and workflows that match your specific operational needs while maintaining visibility across all processes.
Common process analysis platforms and software.
The right tools make process analysis faster and more accurate. Here’s how different platforms support your analysis efforts:
Modern work management platforms like monday work management combine multiple capabilities in one system, a crucial benefit when 57% of employees report an increase in the number of software tools used compared to the previous year. You get process mapping, performance tracking, and improvement implementation without switching between tools.
Key features that support process analysis:
- Visual workflow builders: Create process maps directly in your work platform
- Automated data collection: Track metrics without manual effort
- Real-time dashboards: See process performance instantly
- Integration capabilities: Connect all your tools for complete visibility
Key challenges and solutions.
Every organization faces obstacles during process analysis. Recognizing these challenges helps you prepare solutions in advance.
- Stakeholder resistance: People fear change or worry about job security. Build trust by involving them in analysis and emphasizing improvement over criticism, especially since there’s often a disconnect between how change is perceived; while 45% of senior leaders believe change is managed ‘very well,’ only 23% of individual contributors agree.
- Incomplete data: Missing information makes analysis difficult. Start with what you have and improve data collection over time.
- Process complexity: Interconnected workflows can overwhelm analysis efforts. Break large processes into smaller segments for manageable examination.
- Limited resources: Analysis takes time and expertise. Focus on high-impact processes first and consider bringing in experienced facilitators for complex initiatives.
- Sustaining improvements: Initial gains often fade without ongoing attention. Build monitoring and continuous improvement into your regular operations.
monday work management addresses these challenges with collaborative features like real-time commenting and @mentions that bring stakeholders into the conversation.
Automated tracking captures process metrics without manual data entry, and built-in, customizable dashboards allow you to visualize bottlenecks.
The platform’s workflow automation reduces complexity by standardizing repetitive tasks, while its intuitive interface requires minimal training — making it accessible even with limited resources.
Transform your processes with modern work management.
Process analysis creates the foundation for operational excellence. But lasting improvement requires systems that support continuous optimization and adaptation.
Modern platforms enhance traditional analysis by providing real-time visibility and automated insights. You can spot issues faster, test improvements quickly, and maintain gains over time.
monday work management brings AI-powered capabilities to process analysis:
- Automated bottleneck detection: AI identifies where work slows down
- Predictive analytics: Anticipate problems before they occur
- Intelligent routing: Automatically direct work to the right person
- Smart suggestions: Get recommendations for process improvements
These features transform one-time analysis projects into ongoing optimization systems. Your processes continuously improve based on real data and intelligent insights.
Ready to revolutionize how you analyze and optimize your business processes? Get Started with monday work management today.
Try monday work managementFAQs about process analysis
What is a process analysis example?
A process analysis example could be examining how customer orders move through your fulfillment system. You'd map each step from order placement to delivery, measure how long each stage takes, identify where delays occur, and implement improvements like automated order routing or streamlined picking procedures.
What are the steps of process analysis?
The steps of process analysis include identifying the target process, gathering and mapping current workflow data, evaluating efficiency metrics, pinpointing specific bottlenecks, proposing targeted improvements, implementing changes systematically, and monitoring results for continuous refinement. This structured approach typically takes 2-8 weeks depending on process complexity.
What is the difference between process analysis and business analysis?
Process analysis focuses specifically on examining and improving individual workflows and operational procedures. Business analysis encompasses broader organizational activities including strategy development, requirements gathering, and system design, with process analysis serving as one component within the larger business analysis discipline.
How long does process analysis typically take to complete?
Process analysis duration varies based on workflow complexity and scope, typically ranging from a few days for simple administrative processes to 8-12 weeks for complex cross-departmental workflows. Factors affecting timeline include number of stakeholders involved, data availability, and depth of analysis required.
Can small businesses benefit from formal process analysis?
Small businesses gain significant value from process analysis because it helps them establish scalable workflows before inefficiencies become embedded in operations. Even basic process mapping and improvement can reduce costs, improve customer satisfaction, and create foundations for growth without requiring extensive resources.
What skills are needed to conduct effective process analysis?
Effective process analysis requires analytical thinking to identify patterns and root causes, communication skills to engage stakeholders and gather accurate information, and basic project management abilities to coordinate analysis activities. While industry expertise helps, the core methodology can be learned and applied across different business contexts.
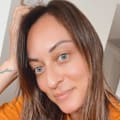