When you’re making a physical product, the name of the game is to minimize waste, and that’s what Lean project management is all about.
The great news is that the project management crusade against waste is winning.
Wasted investment due to poor project performance — missed deadlines, overshot budgets, and scope creep, for example — declined to 9.4% from 11.4% in 2020.
One of the ways manufacturing organizations have minimized waste is by adopting the Lean methodology.
In this article, we’ll define exactly what that means, plus its benefits, principles, and how you can get started using it today.
What is the Lean project management methodology?
Lean project management methodology is a business philosophy, not just a toolset. Its primary goal is to minimize waste of resources and time, all in the name of optimizing your manufacturing process.
When you ultimately implement Lean project management methodology across your business teams effectively, you reduce costs and lead time and increase the quality of your final product.
The “Lean” concept originates with Toyota.
Toyota wanted to ultimately eliminate 3 types of deviations within the Toyota production system.
These 3 deviations included:
- Muda: processes that aren’t valuable or are now outdated and useless
- Mura: waste caused by inconsistency or unevenness
- Muri: any unreasonable burdens that cause stress or burnout within a team
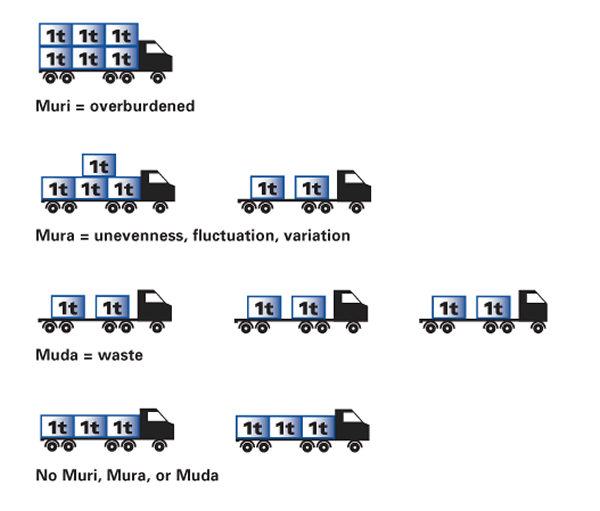
When you remove Muda, Mura, and Muri from your processes, you’re ultimately left with a project management system that follows Lean project management methodology principles.
What does Lean project management mean to the manufacturing industry?
Specifically for companies in the manufacturing space, a Lean manufacturing system reduces the amount of all types of resources needed to get a project made.
This includes:
- Humans: where can you reduce the amount of human effort within a factory?
- Floor space: where can you consolidate the amount of room it takes to make or store your product?
- Tools: do you really need all of the tools you currently use to make your product?
- Engineering hours: how can you streamline processes to produce new products faster?
But, it’s worth reiterating here that none of this should come at the cost of quality.
Lean manufacturing should ultimately result in less inventory and happier customers. It’s meant to trim down bulky processes that have gotten out of hand, not cut corners when it comes to production.What are the benefits of taking a Lean approach to project management?
Taking the Lean approach to project management in the manufacturing industry has a ton of benefits — all of which boil down to lower costs and a better product.
When your Lean manufacturing process runs Lean and efficient, these are the benefits you can enjoy:
- Fewer defects and rework: when your process isn’t streamlined, mistakes are often made during production, which ultimately causes duplicate work.
- Fewer machine breakdowns: machine maintenance, replacement, and upkeep, are integral parts of the manufacturing process.
- Lower levels of inventory: you know exactly which products you’re making and how many you’ll need, meaning you can keep fewer products on hand.
- Higher stock turnover: because you’ve optimized your manufacturing rates based on sales, you will see higher stock turnover as you make what your customers want to buy.
- Less space: optimization on the manufacturing floor means you need less room to store inventory, fewer people to sit at desks, and less machinery to store.
- Less human resources: when processes are more efficient, you see higher levels of productivity from the staff you have.
- Improved delivery performance: when your manufacturing process is as efficient as possible, you can better predict the time to delivery for products that aren’t ordered often.
- Faster development: of course, when processes run smoother overall, you can make your products much more quickly.
The benefits of Lean manufacturing are plentiful and measurable. In fact, General Electric increased production capacity by 20% and lowered material consumption by 4% with the addition of artificial intelligence in its analysis process.
Principles of Lean manufacturing
The Project Management Institute provides 5 principles of Lean manufacturing for project managers to emulate when implementing the strategy within their organizations.
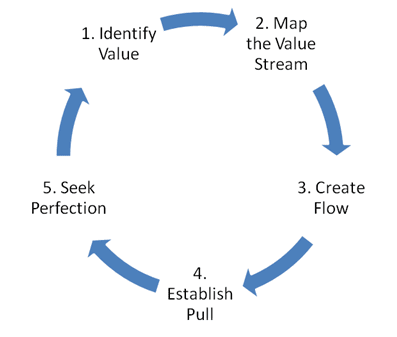
Each Lean manufacturing principle is a step toward Lean thinking. You have to identify what’s important and what’s wasteful in your Lean process.
Let’s go through them one at a time.
1. Specify value in the eyes of the customer
Before you start implementing Lean thinking, you have to pinpoint exactly what creates customer value within your product.
Value is the first Lean principle, and it is defined as the right capability, at the right price, at the right time. Essentially, value is what the customer says, not what you may think.
For example, a furniture manufacturer might assume that many people enjoy their rocking chairs because they’re made of solid oak wood.
But, in fact, many customers desire their particular chair because the arms are so wide, making it easy to rest when rocking a child.
When implementing Lean manufacturing, the organization trimmed down the arms to save on raw materials and lost customers because it failed to pinpoint exactly what made the product valuable in the first place.
2. Identify the value stream for each product
Your value stream is every single action — both those that add value and those that don’t — that you need currently in order to make a product a reality.
This list includes every detail of your manufacturing process — everything from ordering raw materials to switching off the machines at night to save energy. No detail is too small to be recorded and evaluated.
This list of actions is then analyzed during the process of implementing Lean manufacturing. Only the actions that add value are kept. Those that are extraneous often get tossed or adapted so that they do add value.
3. Make value flow by eliminating waste
The central tenets of Lean manufacturing are the elimination of waste and anything that might cause the manufacturing process to stop or pause.
Lean manufacturing should look to build a continuous flow, meaning the process doesn’t get backed up, products don’t get scrapped, and there are no instances of rework or interruptions to the manufacturing process.
In order to achieve this, you analyze your identified value streams, so they fall into one of the following 3 buckets:
- Value-added work: these are essential to get a product created.
- Value-enabling work: you need these actions to run the current process, but they may be eliminated or adapted in the future so that they create more value.
- Non-value-added work: these are eliminated quickly.
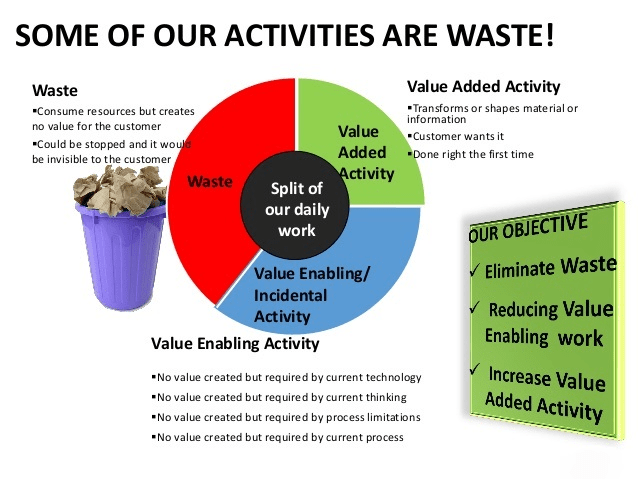
These are the types of actions that are often classified as waste:
- Overproduction: you shouldn’t be manufacturing more products than you need before you need them.
- Waiting: your Lean production process shouldn’t include non-work time like waiting for approval, supplies, or parts.
- Transportation: if you can, avoid the transportation of materials, parts, or finished goods between physical locations or processes.
- Over-processing: don’t do more work than is necessary to make the customer see the value.
- Inventory: don’t keep extra inventory of raw materials, parts, or finished goods.
- Motion: don’t make humans or machines move more than necessary to get the job done.
- Defects: there shouldn’t be any need to repair or rework a product in the process of its making.
4. Let the customer determine the flow
You shouldn’t deliver products before the customer requests or expects them, and you shouldn’t provide a customer with more than what was agreed upon in the initial transaction.
For example, a beauty company may decide to provide a free sample of their new lip gloss with every purchase of their foundation, thinking that if more customers try the lip gloss, they will come back to make a purchase.
The campaign would have the added benefit of delighting the customer by going above and beyond.
In reality, lip gloss sales might not end up being affected by the campaign, and the amount of positive feedback they received from customers could be minimal.
In the end, this beauty company would end up wasting materials as opposed to positively impacting its bottom line.
5. Continuous improvement in the pursuit of perfection
Finally, those looking to implement Lean manufacturing should constantly be evaluating whether or not their actions are providing value and whether or not any actions could be taken to get one step closer to the perfect manufacturing process.
This is referred to as continuous improvement, which is what Lean thinking always tries to achieve.
How to implement Lean manufacturing with monday.com
In order to run Lean, you need a tight grip on inventory and your manufacturing process, all of which can be tracked and monitored with the right Lean manufacturing tool.
Each of the 5 Lean manufacturing practices can be achieved with monday.com.
monday.com is a Work OS (work operating system) that allows you to build custom project management software to suit your business needs. It also allows you to operate more smoothly across manufacturing teams.
For example, you can use features like monday.com automations to automatically order more stock when inventory dips below a certain level.
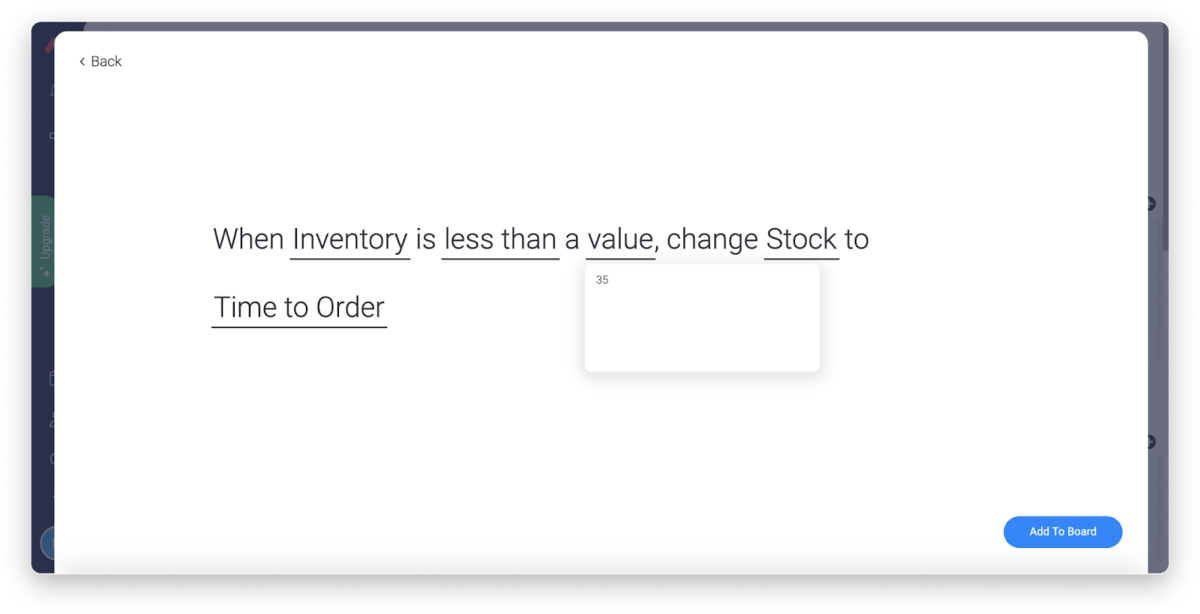
You can adapt monday.com’s workload view to easily visualize the inventory that you have on hand, like this hat manufacturer in the following example:
When certain hats in stock reach a low level, the inventory status is changed from in stock to time to order. By doing this, they never run out, but they also never have too much inventory on hand.
You can use monday.com dashboards to slice and dice inventory management using charts and dashboards, like the one below that displays the number of units on hand for each product:
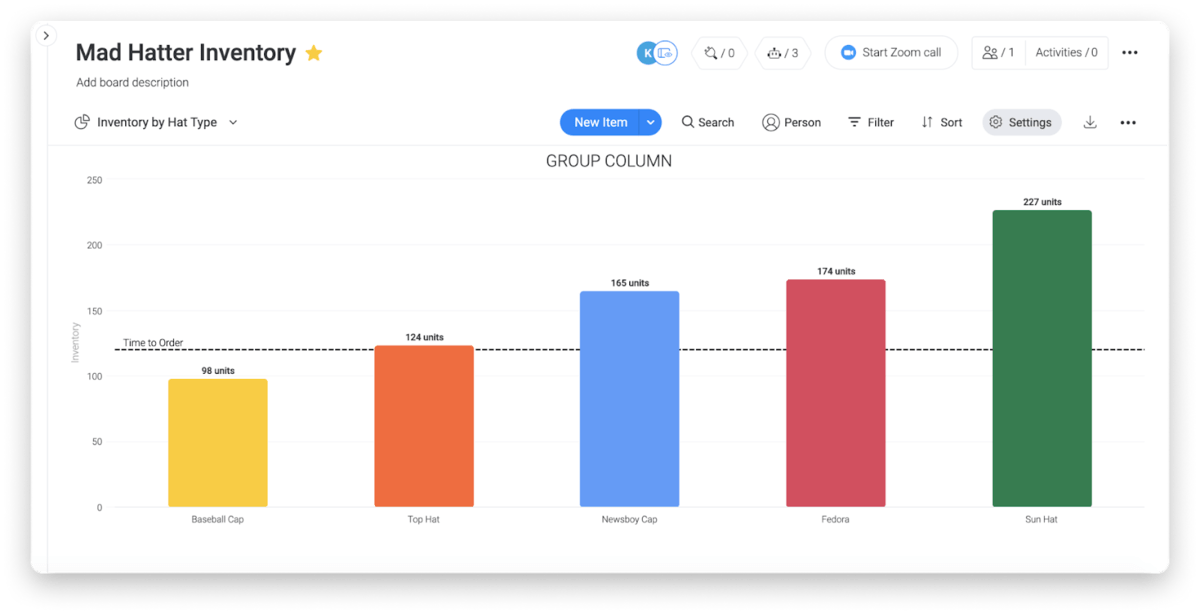
monday.com also provides the capability to keep track of order history so that you always know where customer orders are in the process of being fulfilled.
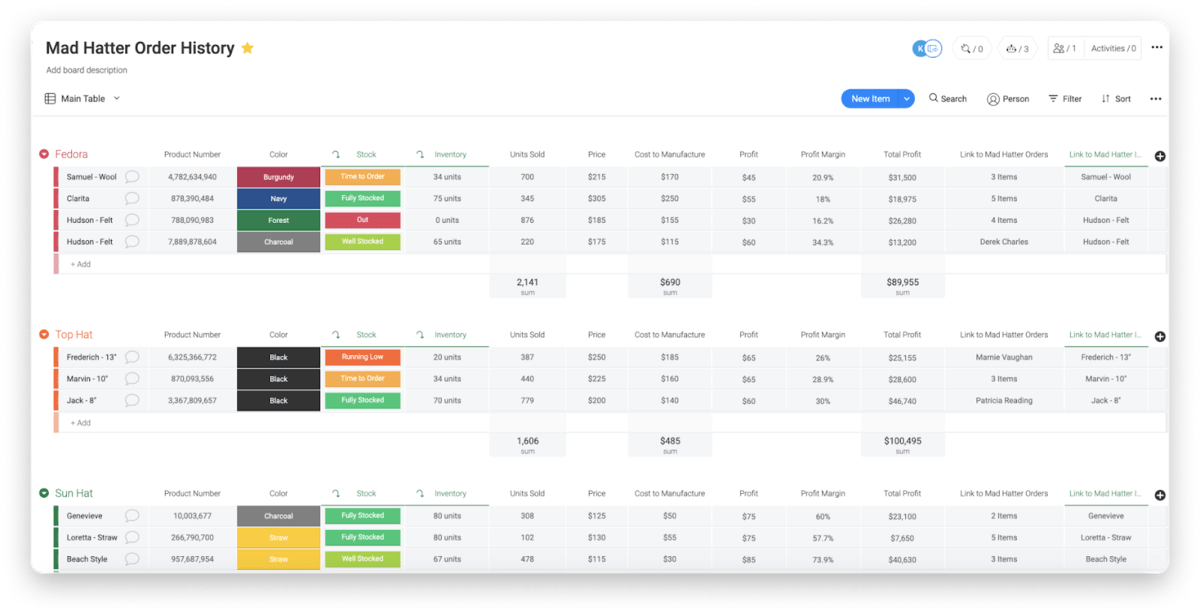
The same dashboard functionality can be used to visualize orders in a variety of ways, like product type or style, or to display order totals to easily see which products are your most popular.
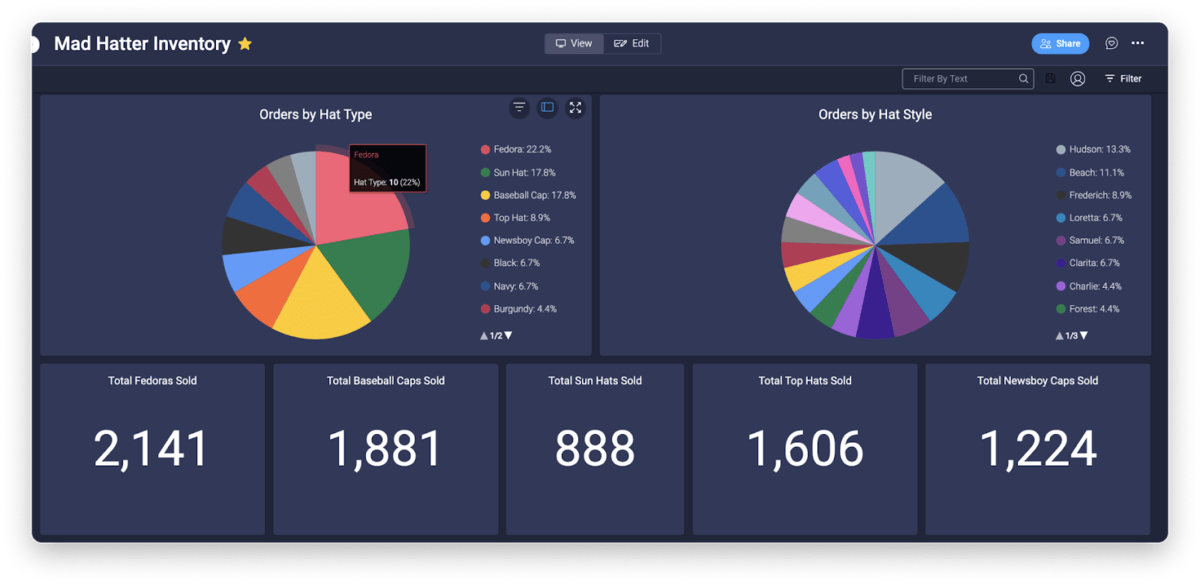
Integrations with over 200 tools allow manufacturing teams to set up automations, effectively eliminating time lags between different stages in Lean production and shipping.
Here’s an example of a set of automations in place between monday.com and a third-party shipping technology that ensures the status of orders is automatically reflected in both places.
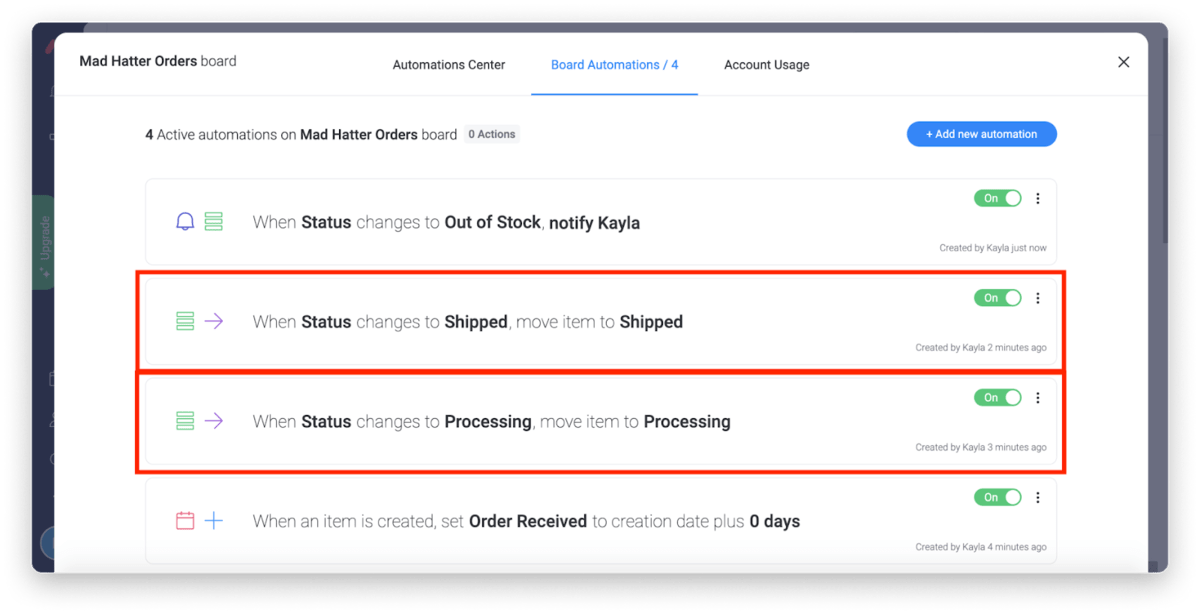
You can visually display shipping requests with monday.com status columns and automate the input of critical data like order received and shipment dates.
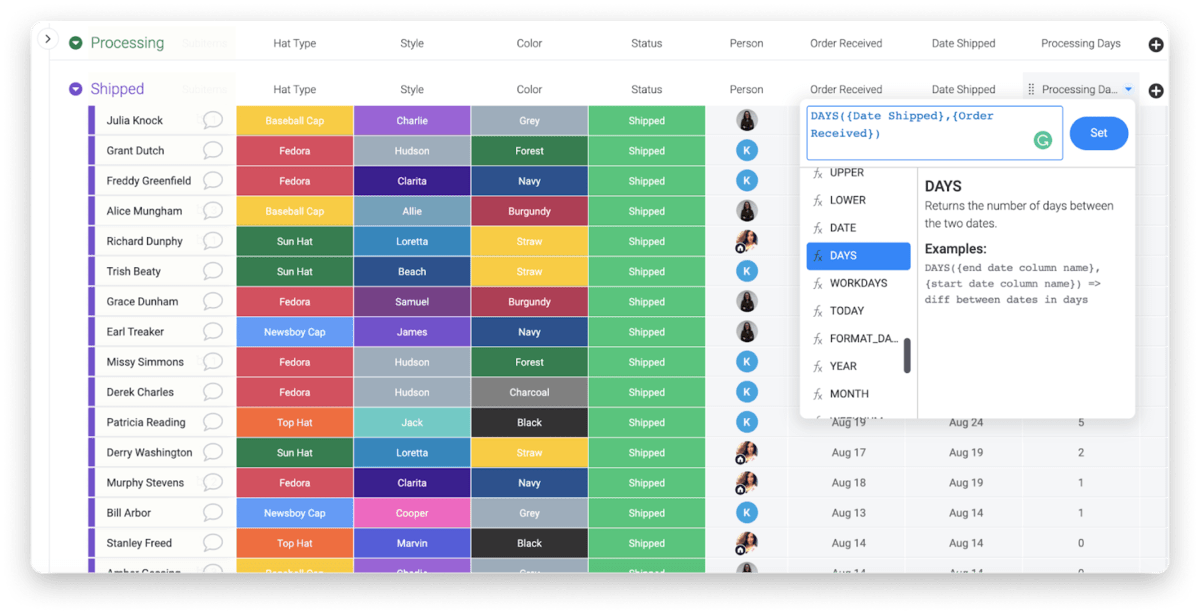
In order to reduce the amount of time it takes to communicate with customers, use monday.com to set up shipping automation emails to alert customers when products are on the way.
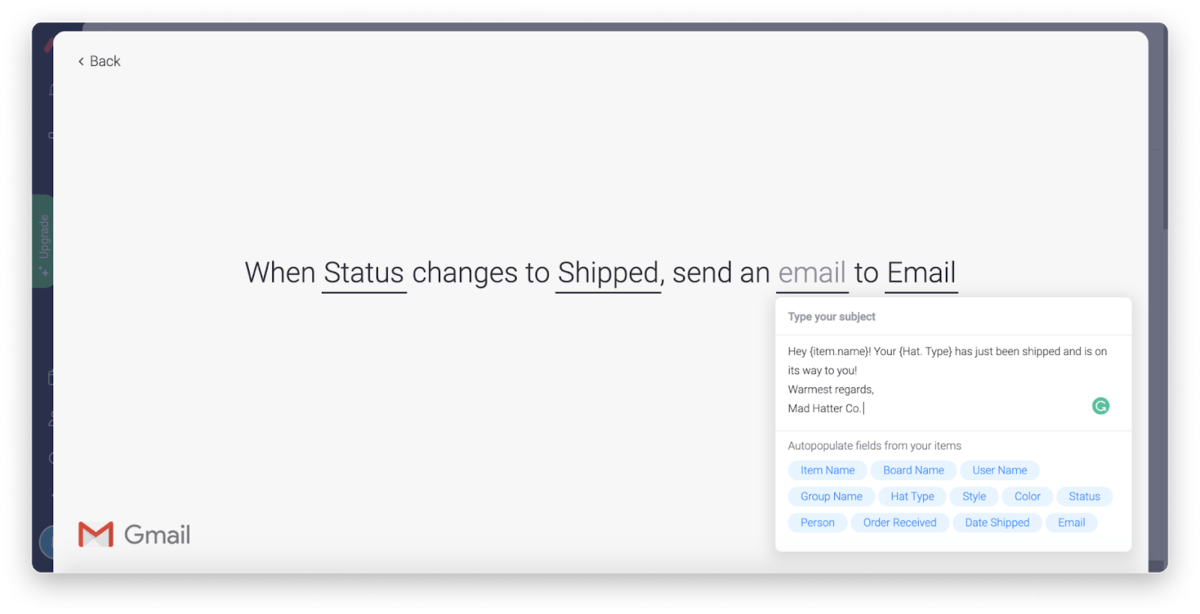
Finally, continuously improve the shipping process by keeping track of how long it takes to process an order on average, profits by product type, and any other metric you may need in your monday.com dashboard.
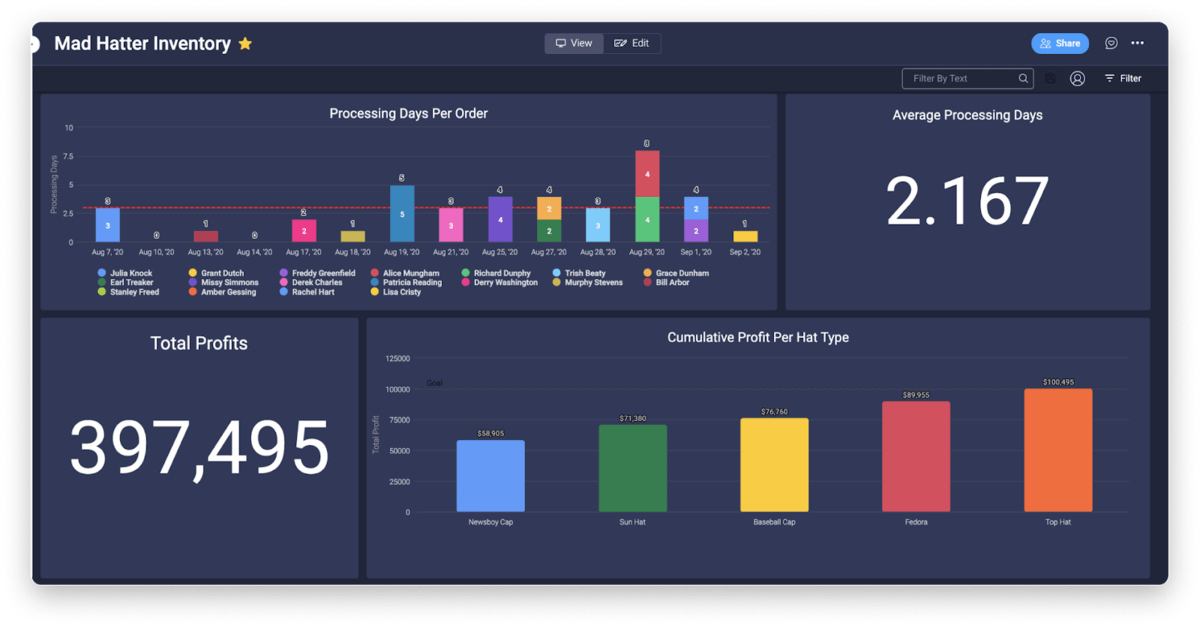
You can link your order history with your contact list as an added feature, so you always have information about which customers have purchased which products on hand.
Lean manufacturing is all about efficiency improvements and waste reduction
The secret to the Lean methodology is transparency and efficient workflows. In order to eliminate waste and inefficient processes, you must be able to see an entire process from start to finish.
If you’re looking for a CRM solution for manufacturing to help you not only identify bottlenecks within your current manufacturing organization but also power collaboration across your entire organization, check out monday.com.