In any growing organization, teams naturally develop their own unique ways to get work done. While this adaptability is a strength, it often creates invisible friction. When everyone follows a different path to the same goal, you get inconsistent outcomes, duplicated effort, and a lot of time spent just figuring out the “how” instead of focusing on the “what”.
This is where process standardization becomes a game-changer. It’s not about rigid rules that stifle creativity, but about creating a clear, shared playbook for your most critical workflows so everyone can execute with confidence.
This guide walks you through everything you need to know, from the core benefits of consistency and a 7-step implementation framework to overcoming common challenges and keeping your processes fresh.
Try monday work managementWhy is standardization important?
Business process standardization is the practice of establishing consistent, uniform procedures across an organization to ensure tasks are performed the same way every time. The standardization def centers on eliminating unnecessary variations in how work gets done, creating predictable outcomes and reducing errors that stem from inconsistent execution.
To explain standardization simply: it’s about creating one proven way to complete important tasks so everyone follows the same approach. When teams operate with standardized processes, they can focus on execution rather than figuring out how to complete tasks.
The ripple effect of consistency
When one department standardizes their processes, it often creates positive pressure for other teams to follow suit, leading to organization-wide improvements in efficiency and collaboration.
Understanding why standardization is important extends beyond operational efficiency. Organizations with standardized processes can more easily identify bottlenecks, measure performance, and implement improvements because they have consistent baselines to work from.
Consistent quality and results you can count on
What does standardization mean for quality control? Standardization creates predictable, reliable results by reducing variations in how work is performed; for example, Ocean Mist Farms reports that using standardized barcodes and data protocols delivered 35% in time savings compared with its previous approach. With a standardized procedure in place, organizations can maintain consistent quality regardless of which team member completes the task.
A standardized system also makes it easier to identify and address issues before they impact quality. When everyone follows the same process, deviations become immediately apparent, allowing for quick corrections.
Improved training and onboarding
Standardizing procedures simplifies training for new employees and makes knowledge transfer more efficient; organizations that lack such consistency often fall into a reactive, ad-hoc model that leads to inefficiencies and inconsistent performance. When processes are documented and standardized, the learning curve is reduced, and teams become less reliant on informal, tribal knowledge.
This approach leads to faster onboarding and fewer mistakes during the transition period. Organizations can also create more effective training materials when they have standardized processes to reference.
Enhanced compliance and risk management
Adhering to process standards helps organizations meet regulatory requirements and manage risks more effectively. Standardization creates an audit trail, making it easier to demonstrate compliance and ensure consistent adherence to policies.
When everyone follows the same documented process, organizations can more easily prove they’re meeting industry standards or regulatory requirements.
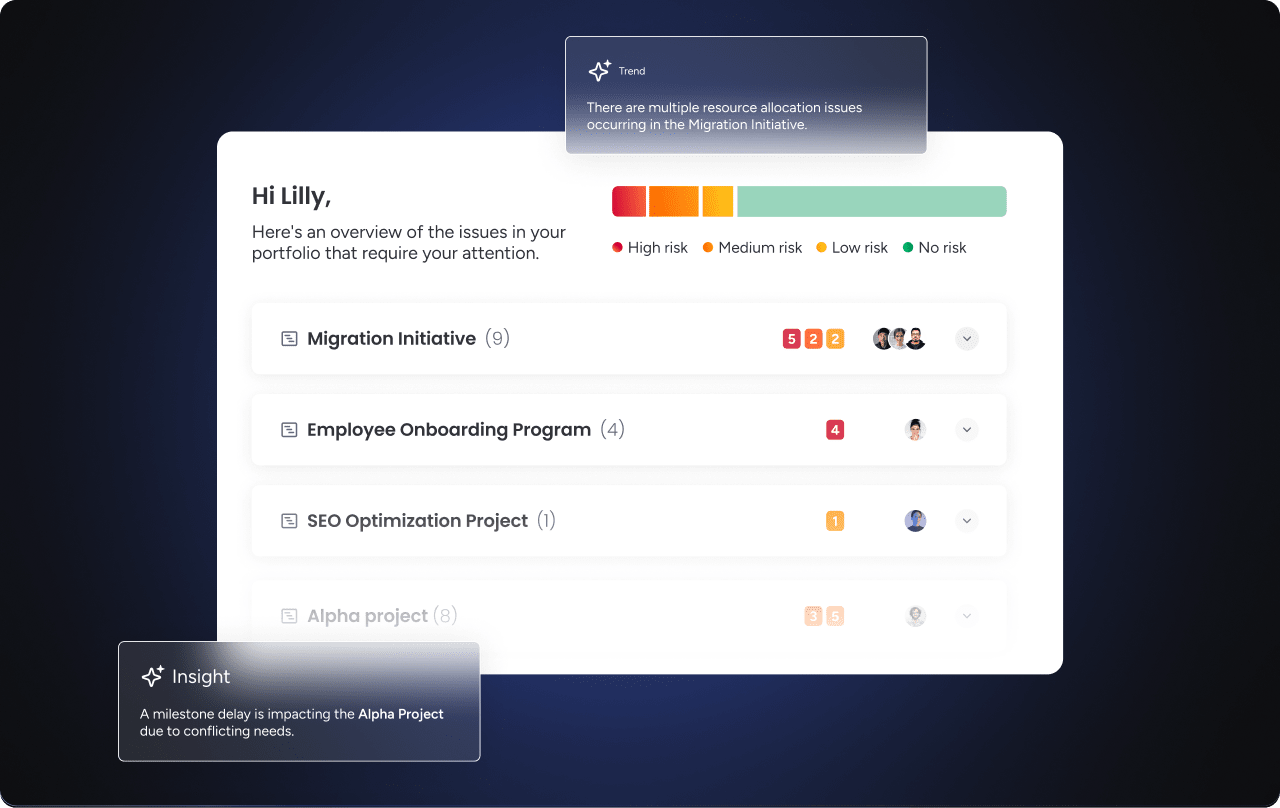
7 steps to standardize process across your organization
The standardization process involves several key steps to ensure your efforts are effective and sustainable across the organization
Organizations that approach standardization methodically see higher adoption rates and more sustainable results. A structured standardization procedure ensures buy-in from stakeholders and creates lastingchange.
Step 1. Identify key processes
Determine which processes to prioritize for standardization by focusing on activities that significantly impact business outcomes. Look for processes that are performed frequently, involve multiple team members, or have high error rates.
Consider the potential impact of standardizing each process. High-impact processes that affect customer experience or regulatory compliance should take priority over internal administrative tasks.
Step 2. Document current workflows
Before standardizing, map out existing workflows to understand how tasks are currently performed across different teams or locations. Document each step, decision point, and handoff using flowcharts, process maps, or workflow diagrams.
Capture both formal procedures and informal workarounds that teams have developed. These workarounds often reveal gaps in existing processes that need to be addressed in the standardized version.
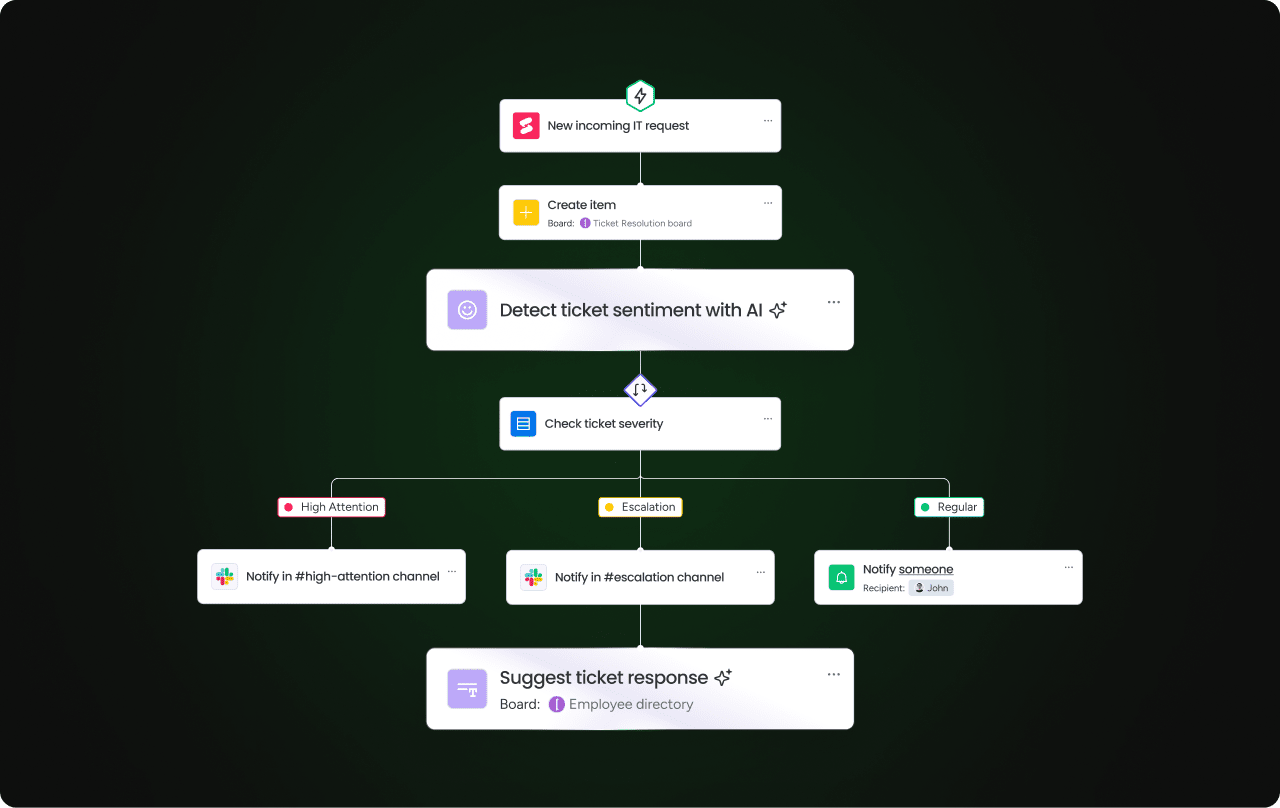
Step 3. Map and analyze variations
Identify differences in how the same process is performed across teams, departments, or locations. Analyze these standardizations to determine which differences are necessary due to unique circumstances and which can be eliminated for greater consistency.
Document the rationale behind each variation to make informed decisions about what to standardize and what to keep flexible. This analysis prevents you from eliminating beneficial adaptations that teams have developed.
Step 4. Create standard procedures
Develop Standard Operating Procedures (SOPs) that are clear, concise, and user-friendly. Write procedures in plain language that anyone can understand, avoiding technical jargon when possible.
Gather input from process users during development to ensure procedures are practical and effective. The people who perform the work daily often have valuable insights about potential improvements.
Step 5. Train and onboard your team
Get team buy-in and train employees on new standardized processes using change management principles. Explain the benefits of standardization and address concerns about how changes will affect daily work.
Emphasize how standardized processes will make their work easier and more predictable. When team members understand the personal benefits, they’re more likely to embrace the changes.
Step 6. Automate wherever possible
Leverage automation to enforce consistent execution of standardized processes without requiring constant manual oversight. Automation reduces the chance of human error and ensures processes are followed exactly as designed.
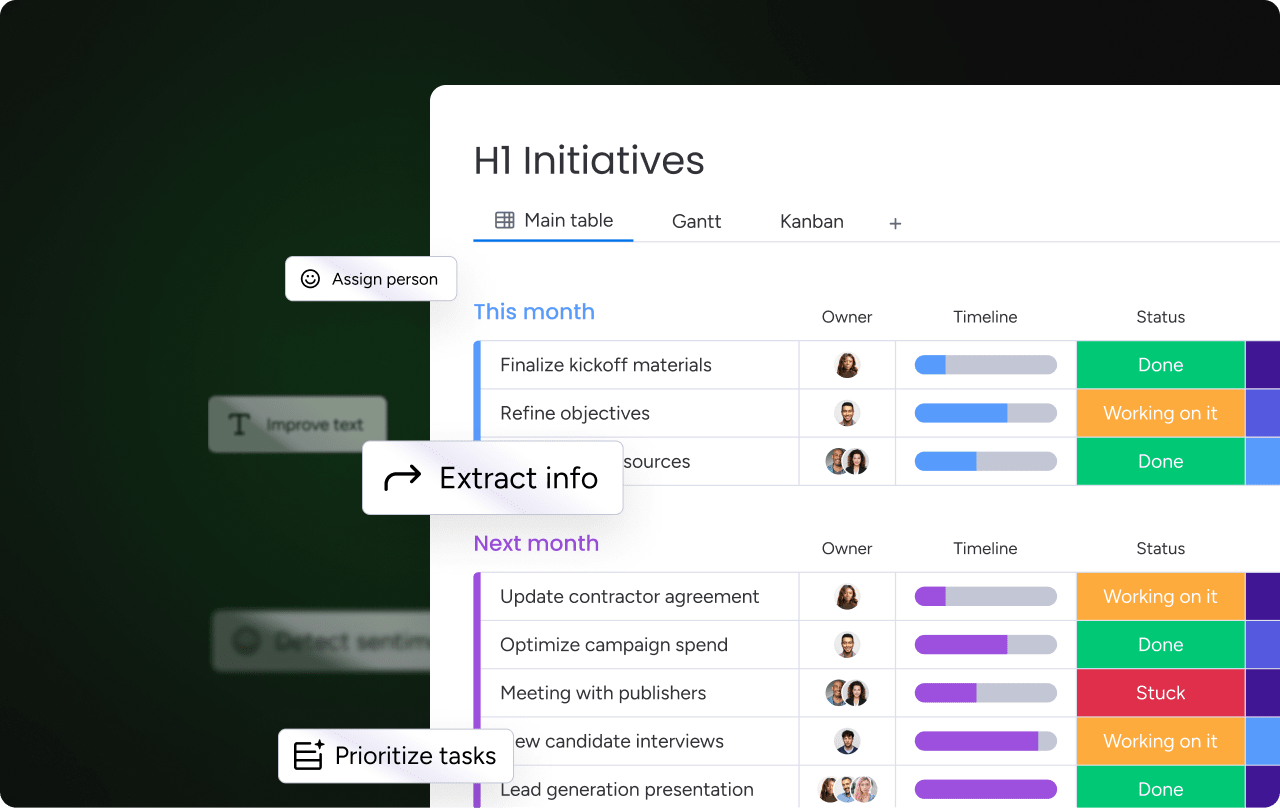
monday work management’s automation capabilities can help maintain standardized processes by triggering specific actions when certain conditions are met. Focus automation efforts on repetitive, rule-based activities that don’t require human judgment.
Step 7. Monitor and refine periodically
Continuous improvement is essential for effective process standardization. Collect feedback from team members and track metrics to evaluate how well standardized processes are working.
Create feedback loops that make it easy for employees to suggest improvements. The most effective standardized processes evolve based on real-world experience and changing requirements.
Try monday work managementCommon challenges and ways to resolve them
Rolling out standardized processes can transform how your teams work, but it’s rarely a smooth ride from day one. Most organizations hit a few predictable bumps along the way. Spotting these challenges early means you can tackle them head-on, turning potential roadblocks into stepping stones for growth.
Here’s a breakdown of the most common hurdles you might face when standardizing processes, especially in service-based environments where flexibility is key, plus actionable ways to clear them:
- Resistance to change: Team members may cling to old habits or worry that new processes will make their jobs harder.Solution: Bring stakeholders into the process design early, and make the benefits crystal clear—show how standardization saves time, reduces errors, and makes daily work more predictable.
- Unclear or overwhelming documentation: If your new procedures are confusing or buried in jargon, people won’t follow them.Solution: Use plain language, step-by-step guides, and visual aids like flowcharts or checklists to make standards easy to grasp and apply.
- Process complexity: Some workflows are naturally intricate, making standardization feel daunting.Solution: Break complex processes into smaller, manageable pieces. Standardize these chunks one at a time, and adjust as you learn what works.
- Inconsistent adoption: Without support, teams may revert to old ways or apply the new process unevenly.Solution: Track how well the new standards are being followed, offer regular training refreshers, and create channels for teams to ask questions or flag issues in real time.
Remember: Standardization isn’t about stamping out creativity or flexibility — it’s about giving your teams a reliable foundation, so they can focus on delivering great results. The most successful efforts treat change management as seriously as process design, turning challenges into opportunities for everyone to level up.
Change management is key
The most successful standardization efforts treat change management as equally important to process design. People need to understand not just what’s changing, but why it matters to them personally.
Types of standardized procedures you can use
Organizations can implement several types of standardization to drive consistency across different aspects of their operations. Understanding what standardization approaches work best helps you choose the right strategy for your specific needs and organizational structure.
Different types of standardization serve different purposes, from ensuring document consistency to improving resource allocation. The key is selecting the approaches that align with your most pressing business needs and will deliver the most significant impact.
monday work management supports multiple standardization approaches through its flexible platform design. What standardization means in practice depends on which type you choose to implement first.
Document-based standard systems
Document templates, forms, and checklists create consistency in how information is captured, processed, and shared across the organization. Standardized documents ensure everyone collects the same information in the same format, making it easier to analyze data and make decisions.
These systems work particularly well for processes that involve information gathering or decision-making based on specific criteria. They provide structure while still allowing for customization based on unique circumstances.
Communication protocols
Standardizing communication channels, formats, and frequency improves clarity and reduces misunderstandings across teams. This includes establishing when to use email versus instant messaging, how to structure project updates, and what information to include in status reports.
Communication protocols become especially important in remote or hybrid work environments where informal communication opportunities are limited. Standardized approaches help maintain connection and alignment across distributed teams.
Resource allocation methods
Standardizing how resources are assigned to projects or processes improves transparency and ensures decisions are made based on consistent criteria. Resource allocation standards help organizations optimize their investments and avoid conflicts over limited resources.
monday work management’s resource management features support this type of standardization by providing visibility into resource availability and utilization across projects and teams.
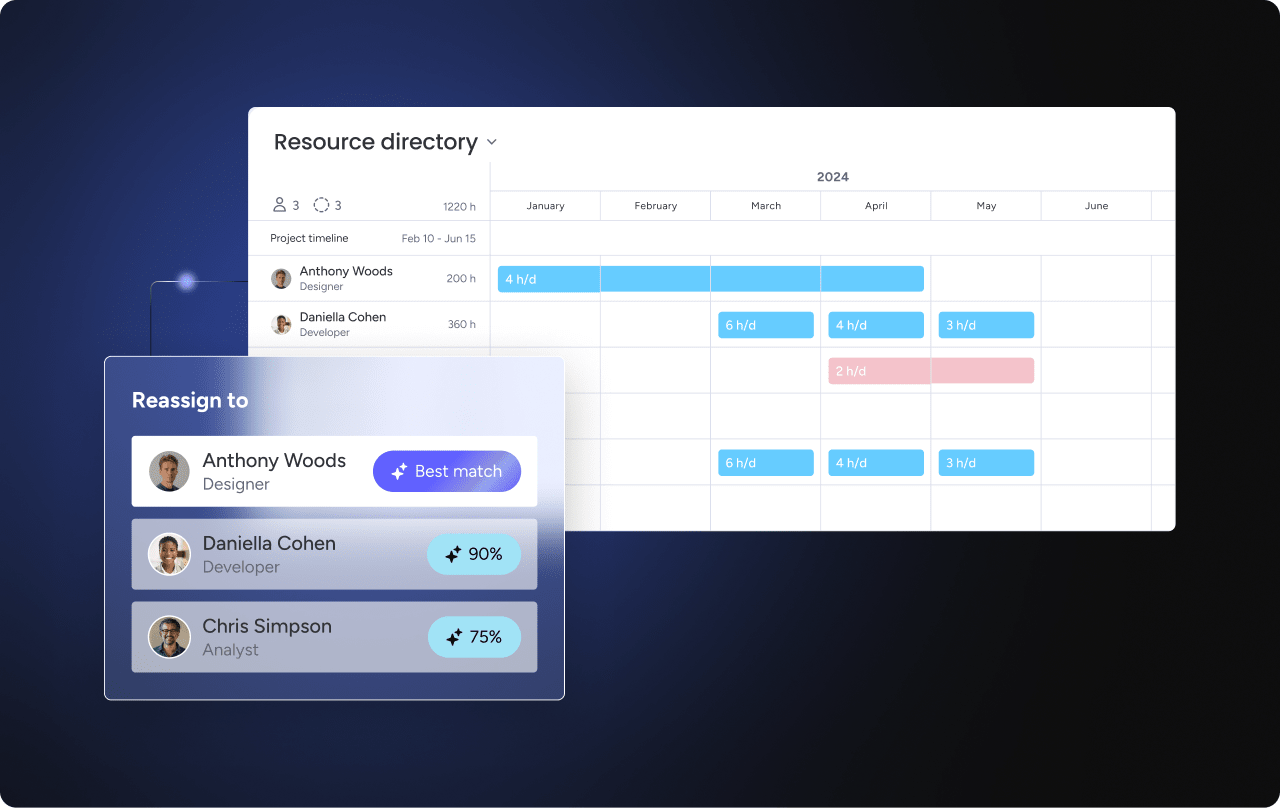
Performance metrics and dashboards
Standardizing KPIs and reporting formats ensures everyone measures success the same way and can compare results across different teams or time periods. When metrics are standardized, organizations can identify best practices and replicate successful approaches in other areas.
Standardized dashboards help ensure stakeholders at different levels receive the information they need in a format they can easily understand and act upon. This creates a standardized output that supports data-driven decision making.
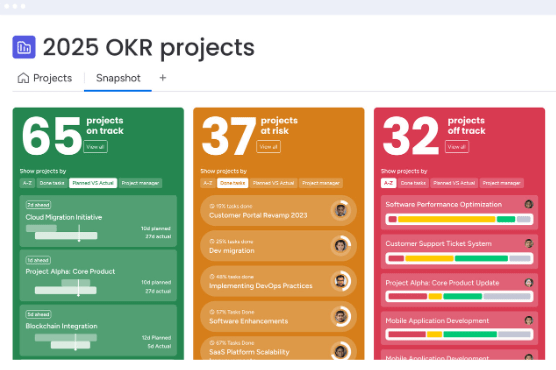
How to ensure continuous improvement
Business process standardization isn’t about creating rigid, unchanging procedures — it’s about establishing a stable foundation that supports ongoing improvement and adaptation. The most successful standardized processes evolve based on feedback, changing business needs, and new opportunities for optimization.
How do you balance consistency with the need for innovation? The key is building flexibility into your standardization approach while maintaining the core elements that drive consistency and quality.
Organizations that treat standardization as a one-time project often find their processes become outdated and less effective over time.
Signals that a standardized process needs updating include:
- Frequent exceptions or workarounds: If teams are regularly bypassing the documented process, it’s a sign the standard no longer fits real-world needs.
- Declining performance metrics: When KPIs like speed, quality, or customer satisfaction start to dip, the underlying process may be out of date.
- Employee feedback: Reports of confusion, inefficiency, or frustration indicate that the standard approach isn’t working as intended.
It’s important to tracking these signals proactively so you can update processes before they start impacting overall performance. You can do this through:
Ongoing feedback loops
Create systems for collecting and acting on feedback about standardized processes from the people who use them daily. Make it easy for employees to suggest improvements and ensure their input leads to meaningful changes when appropriate.
The most valuable feedback often comes from frontline employees who see how processes work in practice. Their insights can reveal gaps between how processes are designed and how they actually function in real-world situations.
Regular innovation sprints
Schedule periodic reviews of standardized processes to prevent stagnation and identify opportunities for improvement. These innovation sprints bring together process users, stakeholders, and subject matter experts to evaluate current performance and brainstorm enhancements.
Innovation sprints work best when they have clear objectives and time boundaries. This focused approach generates actionable improvements without disrupting daily operations or overwhelming teams with too many changes at once.
Try monday work managementBuild consistency in real time with monday work management
monday work management supports process standardization efforts by providing features that align with the best practices discussed throughout this guide. The platform helps teams build, maintain, and improve standardized processes while providing the flexibility needed for continuous improvement.
The platform’s visual approach makes it easier for teams to understand and follow standardized processes. When procedures are represented visually through workflows and dashboards, adoption rates typically improve because team members can quickly grasp what they need to do.
Key features that support standardization include
- Customizable templates that provide starting points for standardized processes, automation capabilities that enforce consistent execution,
- Visual workflows that make standards easy to understand and follow — a critical advantage when 82% of employees already rely on work/project management software to track tasks and collaborate.
- The platform’s dashboards support ongoing monitoring of standardized processes, helping organizations track adoption and identify areas for improvement.
monday work management’s AI capabilities can further enhance standardization efforts through AI Blocks that automatically categorize data, extract information from documents, and suggest next steps based on standardized procedures. These capabilities help maintain consistency while reducing manual effort and supporting standardized management practices.
What standardization looks like in practice becomes clearer when you have the right platform to support your efforts. Organizations can build standardized processes that adapt to their unique needs while maintaining the consistency that drives results.
FAQs about process standardization
What are the 4 stages of business process standardization?
The four main stages of business process standardization are documenting current processes, analyzing variations across teams, creating standard procedures, and implementing with continuous improvement. Each stage builds on the previous one to ensure comprehensive standardization across the organization.
How can organizations measure process standardization success?
Organizations can measure process standardization success through reduced process variation, decreased error rates, improved cycle times, and increased employee satisfaction. Both quantitative metrics and qualitative feedback from process users provide valuable insights into standardization effectiveness.
What is a standardization example in manufacturing industries?
A standardization example in manufacturing is using standardized assembly procedures or quality control protocols to ensure every product meets the same specifications. This includes standardized work instructions, inspection checklists, and safety procedures that create consistent output.
How does business process standardization differ from process improvement?
Business process standardization creates consistency in existing processes by establishing uniform procedures, while process improvement focuses on making processes more efficient or effective. Standardization often serves as a foundation that enables more targeted improvement efforts.
Why is there difficulty of standardizing services compared to products?
The difficulty of standardizing services stems from their inherent variability, high levels of customer interaction, and the need for personalization based on individual client requirements. However, service frameworks can still provide consistency while allowing necessary flexibility for customer needs.
How long does implementing standardized processes typically take?
Implementing standardized processes varies based on process complexity, organizational size, and the scope of changes required. Simple processes may take a few weeks to standardize, while complex, organization-wide initiatives can take several months to fully implement and achieve widespread adoption.
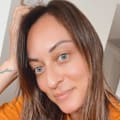