A successful supply chain depends on seamless coordination between dozens of partners, teams, and processes. When everyone works from different spreadsheets and systems, information gets lost, creating delays and risks that can ripple all the way to the customer.
Strong supply chain management transforms this scattered work into a streamlined, transparent operation where everyone is aligned. By centralizing workflows on a platform like monday work management, teams gain the confidence that comes from real-time visibility and clear accountability.
This article walks through everything you need to know to master your supply chain. We will cover the core definition and processes, common challenges and their solutions, and the key benefits of getting it right. We will also explore different SCM models and show how your teams can use modern technology to drive innovation and stay ahead.
Try monday work managementWhat is supply chain management (SCM)
Supply chain management (SCM) is the coordination of all activities involved in sourcing, producing, and delivering products to customers, ensuring maximum value at every step. The supply chain management definition encompasses everything from raw material procurement to final product delivery, creating a seamless flow that connects suppliers, manufacturers, and customers.
What is supply and chain management in practical terms? It’s the strategic oversight of materials, information, and finances as they move through interconnected business processes. The meaning of SCM extends beyond simple logistics to include demand planning, supplier relationships, and risk management across your entire network.
When people ask “what do you know about supply chain management?”, the answer involves understanding how each component works together. The process includes procurement, operations, logistics, distribution, and integration — all coordinated through digital platforms that provide real-time visibility and control.
The supply chain management process
The supply chain management process follows a systematic approach that transforms raw materials into finished products delivered to customers. This process begins with demand forecasting and ends with customer satisfaction, creating value at each stage.
Organizations typically follow three core steps to explain supply chain management effectively
- Establish supplier relationships and procurement strategies based on quality, cost, and reliability to ensure a solid foundation for sourcing materials.
- Coordinate production and operations to align with demand, all while maintaining optimal inventory levels for efficiency and cost control.
- Manage distribution and logistics to guarantee timely delivery to customers and keep operational costs in check.
monday work management enables teams to visualize and coordinate each step of this process through customizable workflows that adapt to any industry or business model.
Supply chain management vs. project management
Supply chain management and project management serve different organizational purposes, though they often work together. Project management focuses on specific initiatives with defined start and end dates, while supply chain management involves ongoing processes that support continuous operations.
The key difference lies in scope and duration. Project management might handle a new product launch or facility expansion, while supply chain management ensures daily operations run smoothly. Both disciplines require coordination, planning, and resource management, but supply chain management operates continuously rather than in discrete project phases.
What is supply chain software
Supply chain software provides digital platforms for managing complex networks of suppliers, manufacturers, and distributors from a centralized location. These platforms integrate data from multiple sources to provide real-time visibility into inventory levels, supplier performance, and delivery schedules.
Modern supply chain software uses no-code building blocks that enable teams to design custom workflows without extensive technical knowledge. Whether managing daily operations or large-scale logistics, these platforms provide the flexibility to adapt to changing business requirements while maintaining operational control.
What challenges does supply chain management address?
Supply chain management addresses critical business challenges that can impact profitability, customer satisfaction, and competitive positioning. These challenges become more complex as organizations grow and expand into new markets or product lines.
Understanding SCM in terms of problem-solving reveals its strategic importance. Organizations face interconnected challenges that require coordinated responses across multiple departments and external partners.
Resource allocation
Resource allocation ensures optimal use of people, materials, equipment, and financial assets throughout your supply network. Effective allocation prevents waste while ensuring adequate resources are available when and where needed.
Supply management involves balancing competing demands for limited resources while maintaining service levels and controlling costs. This requires real-time visibility into resource availability, demand patterns, and capacity constraints across your entire operation.
User accountability
Clear accountability structures ensure team members understand their responsibilities and deadlines within supply chain operations. When everyone knows their role, organizations can maintain consistent performance and respond quickly to changing conditions.
Accountability systems track individual and team performance against established metrics, enabling continuous improvement and rapid problem resolution. This clarity prevents delays and ensures smooth handoffs between different stages of the supply chain process.
Budget restrictions
Budget management within supply chains requires balancing cost control with service level requirements. Organizations must optimize spending across procurement, operations, and logistics while maintaining quality and delivery standards.
Effective budget management involves forecasting costs, tracking actual spending, and identifying opportunities for cost reduction without compromising performance. This financial discipline supports long-term sustainability and competitive pricing.
Siloed teams
Cross-functional collaboration eliminates information silos that can disrupt supply chain operations. When departments share information freely, organizations can make informed decisions and respond quickly to market changes.
Breaking down silos requires establishing communication channels, shared metrics, and collaborative workflows that connect all stakeholders. monday work management facilitates this collaboration by providing shared visibility into supply chain status and enabling real-time coordination across teams.
What are the main benefits of supply chain management?
Effective supply chain management delivers measurable benefits that directly impact organizational performance and competitive positioning. These benefits compound over time as processes mature and teams develop expertise in managing complex networks.
The supply chain management explanation of value creation involves multiple interconnected advantages that support both operational excellence and strategic objectives.
Improves collaboration
Supply chain collaboration creates transparency that enables informed decision-making across all stakeholders. When everyone has access to current information, teams can coordinate activities and resolve issues before they impact customers.
This transparency extends beyond internal teams to include suppliers, logistics partners, and customers, and it resonates with today’s workforce — 81% of employees globally say they’re satisfied when their organization communicates openly. Shared visibility into schedules, inventory levels, and performance metrics enables proactive management and continuous improvement throughout the network.
Reduces bottlenecks and delays
Proactive planning and communication help organizations anticipate and resolve potential bottlenecks before they disrupt operations. This forward-thinking approach maintains smooth workflows and consistent delivery performance.
Identifying bottlenecks requires real-time monitoring of key performance indicators and automated alerts when metrics deviate from normal ranges. Quick response capabilities enable teams to implement solutions before minor issues become major disruptions.
Delivers superior results for clients
Supply chain visibility enables organizations to track progress and adjust operations to maintain high service levels. This capability ensures consistent customer experiences and builds long-term loyalty through reliable performance.
Visual dashboards and automated reporting provide insights into delivery performance, quality metrics, and customer satisfaction scores. These insights enable continuous improvement and proactive customer communication about potential issues.
Try monday work managementWhich SCM teams can benefit from a work management solution?
Supply chain management involves multiple departments that must coordinate their activities to achieve shared objectives. Each team contributes unique expertise while working toward common goals of customer satisfaction and operational excellence.
Teams across the organization benefit from integrated supply chain management platforms that provide role-specific information while maintaining overall visibility. This coordination ensures alignment between departmental objectives and supply chain performance.
Key teams that leverage supply chain management platforms include:
- Operations: Coordinate production schedules and capacity planning
- Procurement: Manage supplier relationships and contract negotiations
- Logistics: Optimize transportation routes and warehouse operations
- Finance: Track costs and manage budgets across the supply network
- Customer service: Provide accurate delivery information and resolve issues
How to execute SCM processes on monday work management
Supply chain management encompasses multiple interconnected processes that organizations can streamline using monday work management. It provides the flexibility to design custom workflows for any supply chain process while maintaining visibility across the entire network.
The definition of supply chain management includes these core processes that monday work management supports:
- demand planning: forecast customer requirements and align resources accordingly
- Supplier management: Track performance, manage contracts, and coordinate deliveries
- Inventory optimization: Balance stock levels with carrying costs and service requirements
- Logistics coordination: Manage transportation, warehousing, and distribution activities
- Performance monitoring: Track key metrics and identify improvement opportunities
monday work management’s no-code building blocks enable teams to create workflows that match their specific requirements while integrating with existing systems and processes.
Try monday work managementGain visibility into core business processes with these monday work management features
monday work management provides comprehensive features that address the complex requirements of modern supply chain operations. These capabilities work together to create a unified platform for managing all aspects of your supply network.
The platform’s customizable design ensures teams have access to the specific functionality they need while maintaining integration across different processes and departments. Key features that support supply chain management include:
- multiple views: visualize supply chain data using Kanban boards, Gantt charts, calendars, and custom dashboards that match your workflow preferences
- Real-time tracking: Monitor inventory levels, supplier performance, and delivery schedules with automatic updates and alerts
- Custom workflows: Design processes that match your specific supply chain requirements using drag-and-drop building blocks
- Automation: Eliminate manual tasks through conditional logic that triggers actions based on predefined criteria
- Integration capabilities: Connect with existing supply chain software and external systems through APIs and pre-built connectors
Approaches and models for SCM supply
Different supply chain models address varying business requirements, market conditions, and risk tolerances. Selecting the appropriate model depends on your industry characteristics, customer expectations, and competitive environment.
What is the scm approach that works for your organization? The answer depends on balancing efficiency, flexibility, and resilience based on your specific operating environment.
Many organizations combine elements from multiple models to create hybrid approaches. monday work management supports any supply chain model by providing configurable workflows that adapt as strategies evolve.
Driving innovation with supply chain software and AI
Technology advancement is transforming how organizations manage their supply networks, moving from reactive processes to predictive, automated systems, as 58% of companies report they are actively shifting to data-driven, cloud-enabled supply-chain operations. Artificial intelligence now handles complex analysis tasks that previously required extensive manual effort.
Are you maximizing the potential of modern supply chain technology? AI-powered platforms can predict demand patterns, optimize inventory levels, and identify potential disruptions before they impact operations.
Step 1: automate repetitive tasks
Automation eliminates time-consuming manual processes while reducing errors and freeing teams to focus on strategic activities. Common automation opportunities include order processing, inventory updates, and performance reporting.
monday work management’s automation capabilities handle routine supply chain tasks while maintaining full visibility into operations. These automations can trigger based on inventory levels, delivery schedules, or performance thresholds.
Step 2: gain end-to-end visibility
Complete supply chain visibility tracks materials and products from initial sourcing through final customer delivery. This comprehensive view helps identify optimization opportunities and enables rapid response to changing conditions.
Digital platforms integrate data from multiple sources to create unified dashboards that make complex information accessible and actionable. Real-time updates ensure decision-makers always have current information for strategic planning.
Step 3: Enhance decision-making through AI blocks
AI analyzes supply chain data to identify patterns, predict outcomes, and recommend actions—and 86% of IT professionals already leverage AI to streamline these kinds of tasks across their organizations. These capabilities enable more accurate forecasting, optimized resource allocation, and proactive risk management.
monday work management’s AI features help teams analyze supply chain performance and make informed decisions based on comprehensive insights rather than intuition alone. Machine learning algorithms can identify trends and suggest improvements that human analysis might miss.
Try monday work managementNavigate supply chain management beyond 2025
The future of supply chain management will be shaped by emerging technologies, evolving customer expectations, and changing global trade patterns. Organizations that prepare for these changes now will gain significant competitive advantages.
What is a scm strategy that prepares your organization for future challenges? The answer involves building flexibility, embracing new technologies, and developing capabilities that adapt to changing market conditions.
Emerging trends include autonomous logistics systems, blockchain transparency, and predictive analytics that anticipate disruptions. Sustainability requirements will continue expanding as regulations evolve and consumer awareness grows.
monday work management provides the adaptability needed to embrace these changes while maintaining operational excellence. The platform evolves with your organization, supporting new processes and technologies as they emerge.
Supply chain excellence creates lasting competitive advantages through improved customer satisfaction, optimized costs, and increased operational resilience. Organizations that invest in comprehensive supply chain management capabilities position themselves for sustained success in an increasingly complex global marketplace.
FAQs about supply chain management
What does supply chain management do for manufacturing companies?
Supply chain management coordinates all activities from raw material sourcing to finished product delivery for manufacturing companies. It optimizes production schedules, manages supplier relationships, and ensures timely delivery to customers while controlling costs.
What are the 5 basic steps of supply chain management implementation?
The five basic steps are planning demand and supply requirements, sourcing materials and selecting suppliers, manufacturing or production operations, delivery and logistics coordination, and returns management. Each step requires integration with others for optimal performance.
What are the 5 main functions of supply chain management operations?
The five main functions include procurement of materials and services, operations that transform inputs into products, logistics for transportation and storage, distribution to deliver products to customers, and integration that connects all activities through technology and communication systems.
How can small businesses implement supply chain management without large IT budgets?
Small businesses can implement supply chain management using cloud-based platforms that offer scalable pricing and user-friendly interfaces. These platforms provide essential functionality without requiring extensive technical resources or large upfront investments.
Which supply chain management metrics provide the most valuable business insights?
The most valuable metrics include order accuracy rates, lead times from order to delivery, inventory turnover ratios, supplier performance scores, and total supply chain costs as a percentage of revenue. These metrics provide insights into operational efficiency and customer satisfaction.
What distinguishes supply chain management from traditional logistics management?
Supply chain management encompasses the entire network from suppliers to customers, while logistics management focuses primarily on transportation and warehousing activities. Supply chain management includes strategic planning, supplier relationships, and demand forecasting beyond basic logistics operations.
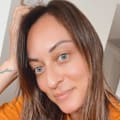